El proceso de producción principal para el cuerpo de una comida de tres piezas puede
El principal proceso de producción para el cuerpo de una lata de alimentos de tres piezas incluyecorte, soldadura, revestimientoyel secadode la costura de soldadura, cuello, brida, cuentas, sellado, prueba de fuga, pulverización y secado completos y empaquetado. En China, la línea de producción automática de CAN generalmente está compuesta por máquinas de ensamblaje de carrocería, máquinas de corte bidireccionales, máquinas de soldadura, protección de costuras de soldadura y sistemas de recubrimiento/curado, sistemas de pulverización/curado de interiores (opcionales), máquinas de detección de fugas en línea, máquinas de apilamiento vacías, máquinas de apilamiento, máquinas de soporte y máquinas de cine de envolturas/envolturas térmicas. Actualmente, la máquina de ensamblaje del cuerpo puede completar procesos como la reducción, el cuello, la expansión, la oleada, el brindación, el abaloramiento, la primera y la segunda costura, a una velocidad de hasta 1200 latas por minuto. En el artículo anterior, explicamos el proceso de corte; Ahora, analicemos el proceso de cuello:
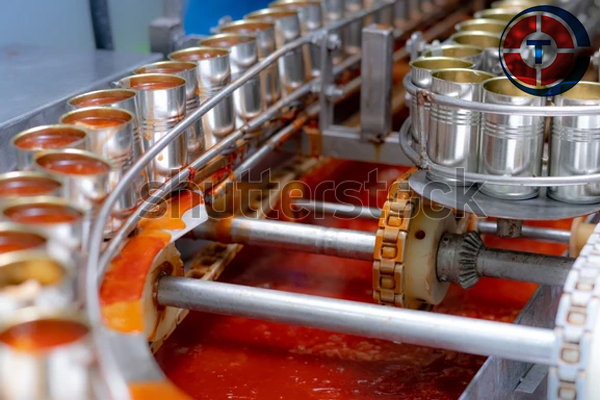
Besuqueo
Un método importante para reducir el consumo de material es adelgazar el hojalata. Los fabricantes de Tinplate han realizado un trabajo significativo a este respecto, pero simplemente adelgazar el hojalata para reducir el costo está limitado por los requisitos de resistencia a la presión de la estructura de lata, y su potencial ahora es bastante pequeño. Sin embargo, con los avances en el cuello, las bridas y la tecnología de expansión de Can, ha habido nuevos avances para reducir el consumo de material, especialmente tanto en el cuerpo de la lata como en la tapa.
La principal motivación para producir latas de cuello fue inicialmente impulsada por el deseo de actualizaciones de productos por parte de los fabricantes. Más tarde, se descubrió que bucear el cuerpo de la lata es una forma efectiva de ahorrar material. El cuello reduce el diámetro de la tapa, reduciendo así el tamaño del blaning. Al mismo tiempo, a medida que la resistencia de la tapa aumenta con el diámetro reducido, los materiales más delgados pueden lograr el mismo rendimiento. Además, la fuerza reducida en la tapa permite un área de sellado más pequeña, reduciendo aún más el tamaño del blaning. Sin embargo, el adelgazamiento del material del cuerpo puede causar problemas debido a los cambios en el estrés del material, como la resistencia reducida a lo largo del eje de lata y la sección transversal del cuerpo de lata. Esto aumenta el riesgo durante los procesos de llenado de alta presión y el transporte por parte de rellenos y minoristas. Por lo tanto, aunque el cuello no reduce significativamente el material del cuerpo de lata, conserva principalmente material en la tapa.
Dada la influencia de estos factores y la demanda del mercado, muchos fabricantes han mejorado y mejorado la tecnología de cuidados, estableciendo su posición única en las diversas etapas de la fabricación de CAN.
En ausencia de un proceso de corte, el cuello es el primer proceso. Después de recubrir y curarse, el cuerpo de lata se entrega secuencialmente a la estación de cuello por el gusano de separación de lata y la rueda de estrella de alimentación. En el punto de transferencia, el moho interno, controlado por una leva, se mueve axialmente hacia el cuerpo de la lata mientras gira, y el moho externo, también guiado por una leva, se alimenta hasta que coincida con el molde interno, completando el proceso de cuello. El molde externo luego se desactiva primero, y el cuerpo de lata permanece en el molde interno para evitar resbalones hasta que alcance el punto de transferencia, donde se desconecta del molde interno y la rueda de la estrella de Outfeed la entrega al proceso de brida. Por lo general, se utilizan métodos de cuello simétricos y asimétricos: el primero se aplica para una lata de 202 diámetros, donde ambos extremos experimentan a las cuestiones simétricas para reducir el diámetro a 200. El segundo puede reducir un extremo de una lata de 202 diámetro a 200 y el otro extremo a 113, mientras que un diámetro de 211 puede reducirse a 209 y 206, respectivamente, después de tres asimmetic necking Operations.
Hay tres tecnologías de cuello principales
- Guarda: El diámetro del cuerpo de lata puede encogerse en uno o ambos extremos simultáneamente. El diámetro en un extremo del anillo de cuello es igual al diámetro del cuerpo de lata original, y el otro extremo es igual al diámetro de cuello ideal. Durante la operación, el anillo de cuello se mueve a lo largo del eje del cuerpo de lata, y el molde interno evita la arrugas y garantiza el cuello preciso. Cada estación tiene un límite sobre cuánto se puede reducir el diámetro, dependiendo de la calidad del material, el grosor y el diámetro de la lata. Cada reducción puede disminuir el diámetro en aproximadamente 3 mm, y un proceso de cuello de múltiples estaciones puede reducirlo en 8 mm. A diferencia de las latas de dos piezas, las latas de tres piezas no son adecuadas para el cuello de moho repetido debido a inconsistencias de materiales en la costura de soldadura.
- Cuidados: Esta tecnología se deriva de los principios de dos piezas de cuello. Permite curvas geométricas suaves y puede acomodar el cuello de múltiples etapas. La cantidad de cuello puede alcanzar 13 mm, dependiendo del material y el diámetro de la lata. El proceso ocurre entre un molde interno giratorio y un molde de formación externo, con el número de rotaciones dependiendo de la cantidad de cuello. Las abrazaderas de alta precisión aseguran la concentricidad y la transmisión de la fuerza radial, evitando la deformación. Este proceso produce buenas curvas geométricas con una pérdida mínima de material.
- Formación de moldes: En contraste con el cuello de moho, el cuerpo de lata se expande al diámetro deseado, y el molde de formación entra desde ambos extremos, dando forma a la curva final del cuello. Este proceso de un solo paso puede lograr superficies suaves, con calidad de material e integridad de la costura de soldadura que determina la diferencia de cuello, que puede alcanzar hasta 10 mm. La formación ideal reduce el grosor de hojalata en un 5%, pero conserva el grosor en el cuello al tiempo que mejora la resistencia general.
Estas tres tecnologías de cuello ofrecen ventajas que dependen de los requisitos específicos del proceso de fabricación de la lata.
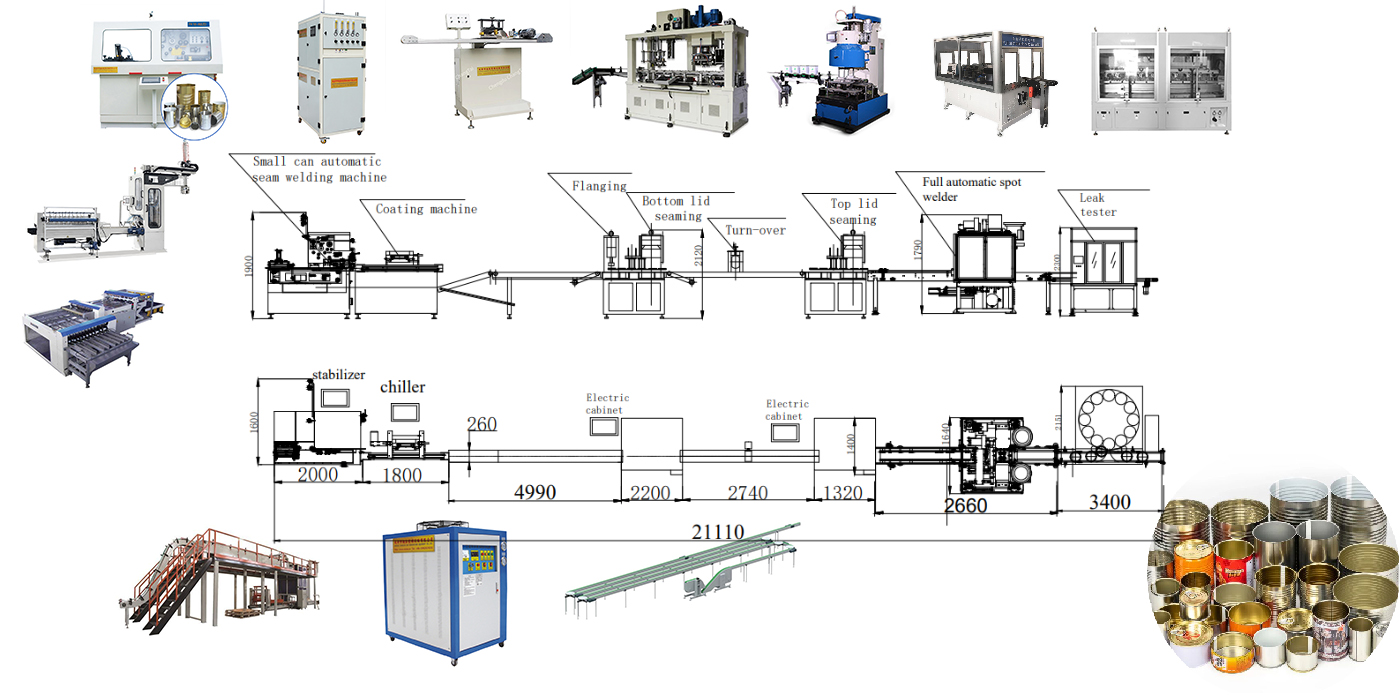
Video relacionado de la máquina de soldadura de lata de lata
Chengdu Changtai Intelligent Equipment Co., Ltd.- Un fabricante de equipos de lata automático y exportador de equipos, proporciona todas las soluciones para TIN CAN. Para conocer las últimas noticias de la industria de embalaje de metales, encuentre una nueva línea de producción de Tin CAN y obtenga los precios sobre la máquina para hacer, elija calidad de calidad CAN Machine en Changtai.
ContáctenosPara detalles de maquinaria:
Tel: +86 138 0801 1206
WhatsApp: +86 138 0801 1206 +86 134 0853 6218
Email:neo@ctcanmachine.com CEO@ctcanmachine.com
Tiempo de publicación: octubre-17-2024